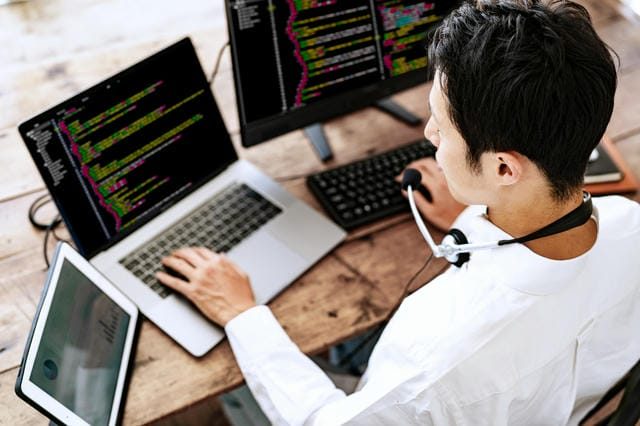
プリント基板は、電子機器の心臓部ともいえる重要なコンポーネントであり、その役割や設計プロセスは多岐にわたる。一般的にプリント基板は、絶縁体の基板に導体が形成され、電子部品が取り付けられる構造をしている。この基板を使用することで、電子回路が物理的に配置され、信号や電力が効率的に流れるようになっている。プリント基板の設計段階では、多くの要因を考慮に入れる必要がある。まず、回路図を基にして、各素子の配置や接続を計画する。
この初期段階での選択が、最終的な基板の性能や信号品質に大きな影響を与える。プリント基板の設計ソフトウェアを使用することで、設計者はリアルタイムで回路のシミュレーションを行うことが可能となり、エラーの早期発見が助けられる。次に、複数の層を持つ基板について考える必要がある。シングル層やダブル層の基板が一般的であるが、複雑な電子機器にはより多くの層を持つ多層基板が必要とされることも多い。多層基板の設計は、層ごとに信号の配線を行い、不要な干渉を避けるための手法が求められる。
この技術により、高密度な配線が可能になり、コンパクトなデバイスの設計が容易になる。次は材料の選定である。プリント基板の素材は、通常、エポキシ樹脂によって作られたガラス繊維強化プラスチックが主流であり、これに金属製のパターンが施される。素材選びは耐熱性や機械的特性に影響を与え、最終的な製品の品質を決定づける要素となる。特に、高い温度で作動する機器では、熱への耐性が求められるため、材料選びは慎重に行われる。
製造面では、プリント基板を手がけるメーカーは、通常、高度な技術と設備を必要とする。基板の製造プロセスは複雑で、多くの工程が含まれる。最初に、設計データを基にして、基板のレイアウトがフォトリソグラフィー技術で転写される。次に、エッチングやメッキ処理が行われ、導体パターンが形成される。これらの工程では、精密機器や化学薬品が使用されるため、品質管理は非常に重要だ。
品質管理といえば、製造プロセスにおいて不良品が出ることは避けられないが、その発生を最小限に抑えるための取り組みは不可欠である。製造メーカーはISO規格などの国際的な基準に準拠し、トレーサビリティを確保するための仕組みを整えることが求められる。不良品が出た際には、原因を突き止め、改善策を講じることが、再発防止の鍵となる。次にプリント基板の実装工程にも触れる。実装とは、印刷された基板に電子部品を実際に取り付ける過程で、手作業や自動機械を用いることが多い。
表面実装技術(SMT)は、部品が基板の表面に面付けされる方式であり、多くの部品を省スペースで配置できる利点がある。この技術の普及により、スピードと精度が求められる現代の電子機器制作に対応している。さらに、プリント基板は製品のライフサイクルにも密接に関係している。例えば、製品の更新やリニューアルが求められる際、基板の改版が必要になることが多い。この場合、製造メーカーは、新しい機能を添加したり、コストを削減したりするために、デザインを見直さなければならない。
このように、電子機器が長期間にわたって競争力を維持するためには、基板技術の進化が欠かせない。また、環境への配慮も重要な視点である。リサイクル可能な素材や低環境負荷の製造プロセスが求められており、プリント基板のメーカーはそれに応じた技術革新を行わなければならない。さらに、市場のニーズに応じて、生産体制や材料の選定を見直す柔軟性も求められる。プリント基板に関連する分野は広がり続け、さまざまな新技術が誕生している。
例えば、フレキシブル基板や高周波対応基板など、特定の用途に特化した製品が求められるようになってきている。これにより、家電から自動車、さらには医療機器まで、幅広い分野で電子回路が使用されていることを実感できる。このように、プリント基板は、設計から製造、実装、さらには製品ライフサイクルまで、多くの側面で非常に重要な役割を果たしている。各工程が密接に関連し合いながら、技術者たちの知恵と努力によって、革新的な製品が生まれている。今後も技術の進歩に伴い、プリント基板に対する要求はますます高度化していくことが予想される。
そのため、継続的な学習と技術向上が求められ、業界全体が進化し続けることが必要である。プリント基板は、電子機器の基盤として非常に重要な役割を果たしている。基板の設計プロセスは、回路図の作成から始まり、素子の配置や接続を計画する段階が含まれる。この初期段階での選択は、最終的な基板の性能や信号品質に影響を及ぼす。設計者は、専用のソフトウェアを用いてリアルタイムで回路のシミュレーションを行い、エラーを早期に発見することができる。
基板にはシングル層や多層構造があり、特に複雑なデバイスには多層基板が求められる。設計では、層ごとの信号配線や干渉の回避が考慮され、コンパクトなデバイスを実現する。材料選びも重要で、エポキシ樹脂やガラス繊維強化プラスチックなどの素材が使用され、耐熱性や機械的特性が最終製品の品質を左右する。製造プロセスは複雑で多くの工程を含む。設計データに基づき、フォトリソグラフィー技術で基板のレイアウトを転写し、エッチングやメッキ処理で導体パターンを形成する。
この過程では品質管理が極めて重要で、国際的な基準に従ったトレーサビリティが求められる。実装工程では、電子部品を基板に取り付ける作業が行われ、表面実装技術(SMT)が多用されている。この技術により、部品を省スペースで配置が可能となり、製品の高納期や高精度な製造が実現されている。また、製品のライフサイクルに伴って基板の改版も求められ、新機能の追加やコスト削減に向けたデザイン見直しが行われる。環境への配慮も重要視されており、リサイクル可能な素材や低負荷の製造プロセスが求められている。
さらに、フレキシブル基板や高周波対応基板など、多様な用途に特化した技術が進化している。電子機器は様々な分野で普及しており、プリント基板の技術進化が不可欠である。このように、プリント基板は設計から製造、実装、製品ライフサイクルまで多面的に重要な役割を担っている。技術者たちの努力によって、革新が続けられ、今後も求められる性能は一層高度化していくことが予想される。業界の進化には継続的な学習と技術向上が欠かせない。